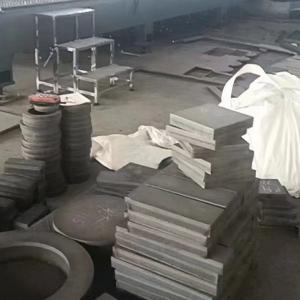
Add to Cart
Custom Cutting Stainless Steel Forged Plate Thickness 10 - 300mm Plasma Cutting Any Size
Item | forged Stainless Steel Plate |
Raw Material | Stainless steel |
Grades | 201, 304, 304L, 310S, 309S, 316, 316L, 321, 409L, 410, 410S, 420, 430, 431,904L, 2205 ,2507,254SMO,253MA,17-4ph.etc. |
Thickness | 10-300mm |
Service | Cutting, polishing |
Width | 1000mm 1219mm 1500mm or cutting any size as your request |
Finish | 2B, BA, No. 1, No. 4, mirror, brush, hairline, chequered, embossed, etc. |
Package | Standard export package |
Regular Thickness of our Plate we can produce
Thickness | 10.0mm 12.0mm 14.0mm 16.0mm 20.0mm 25mm 30mm 35mm 40mm 45mm 50mm 55mm 60mm 65mm 70mm 75mm 80mm 90mm 100mm 110mm 115mm 120mm 130mm 140mm 150mm 160mm 170mm 180mm 190mm 200mm 210mm 220mm 240mm 250mm 300mm |
Type of our foreged stainless steel products
Type | Plate |
Rod | |
Pipe | |
Circle |
Our team can assist you in comparing the pros and cons of these and other stainless steel grades for your project. 300 and 400 series alloys are the most common for manufacturing, but you may also select a 200, 500 or 600 series alloy for your particular application.
There are other grades within each series, which may also offer the unique combination of hardness, heat resistance and corrosion resistance you need.
The 300 series used in stainless steel forging is made of austenitic chromium-nickel alloys. Here are some basic features of common 300 series steel alloys:
These ferritic and martensitic chromium alloys are affordable, easy to work with and come with some unique features between each type. Compare basic 400 series steels to see how you can improve your stainless steel forging process:
In order to better understand the various grades of forging stainless steel, it’s important to understand the basic types of stainless steel and how their structures affect their properties. Most metals have a crystalline lattice structure. Most of the atoms in stainless steel are iron and carbon. Ferritic, austenitic and martensitic are all iron crystal structure options that greatly affect the overall quality of stainless steel.
One of the most important aspects of these structural differences is the amount of carbon the iron structures can absorb. Increased levels of carbon usually lead to harder, more brittle steel. No steel heat treatment perfectly shapes every crystalline structure, so the heating and cooling process can create various structures within the same piece of steel. The characteristics of each series type and grade reflect the overall structure and qualities of a particular alloy.
Ferrite crystals contain the least amount of carbon. A ring of iron atoms form around a single iron atom in the middle, creating very little space for carbon atoms to be absorbed. Most ferritic alloys have average hardness and strength and limited corrosion resistance.
Once ferrite is heated to approximately 912 degrees Celsius, the crystal structures change and are capable of absorbing up to 2% carbon. While this carbon remains in the stainless steel forging alloy at high temperatures, it often reverts to ferritic steel once cooled. Manganese or nickel must be introduced to the metal to hold its carbon and austenitic properties. These properties include high corrosion resistance and hardness.
Quenched steel creates martensite, which is the leading property of martensitic stainless steel forging alloys. Developed by and named after Adolf Martens, a 20th century metallurgist, martensitic steel has excellent hardness and proves to be a popular option for sharp blades. The chemical resistance, however, is less than in austenitic steel.